Demande client
Tracer sans intervention humaine des citernes de levure chimique (liquide) dans un process de production, dans les stocks et lorsqu’elles quittent la société.
Contexte de traçabilité RFID agroalimentaire
Fabricant de levure chimique destinée aux particuliers et aux professionnels, l’entreprise conditionne ses produits dans des citernes de 300 et 1000 Kg, qui sont livrées à ses clients puis récupérées pour être lavées et remplies à nouveau.
Elle est soumise à l’importante exigence de traçabilité demandée au secteur agroalimentaire.
Qualité & sécurité : garantir la traçabilité
En sus de la traçabilité requise, l’entreprise a besoin de sécuriser son process. En effet, il est nécessaire de pouvoir garantir que chaque citerne a bien été soigneusement nettoyée avant d’être remplie à nouveau.
La traçabilité doit aussi permettre d’identifier les citernes nécessitant des réparations.
Productivité : suivi de process en temps réel
L’entreprise recherche une vision temps réel de l’évolution de la production. Cela lui permet de :
- s’assurer à tout moment d’avoir suffisamment de citernes en stock
- gagner en réactivité en cas de problème pour diminuer les arrêts de production.
Diminution charge administrative : automatisation et zéro papier
La mise en place de solutions RFID pour l’industrie agroalimentaire doit permettre de réduire la charge administrative de l’activité. Les informations générées par les systèmes de détection RFID sont stockées directement dans l’ERP (SAP) via une passerelle reliant RFID et ERP.
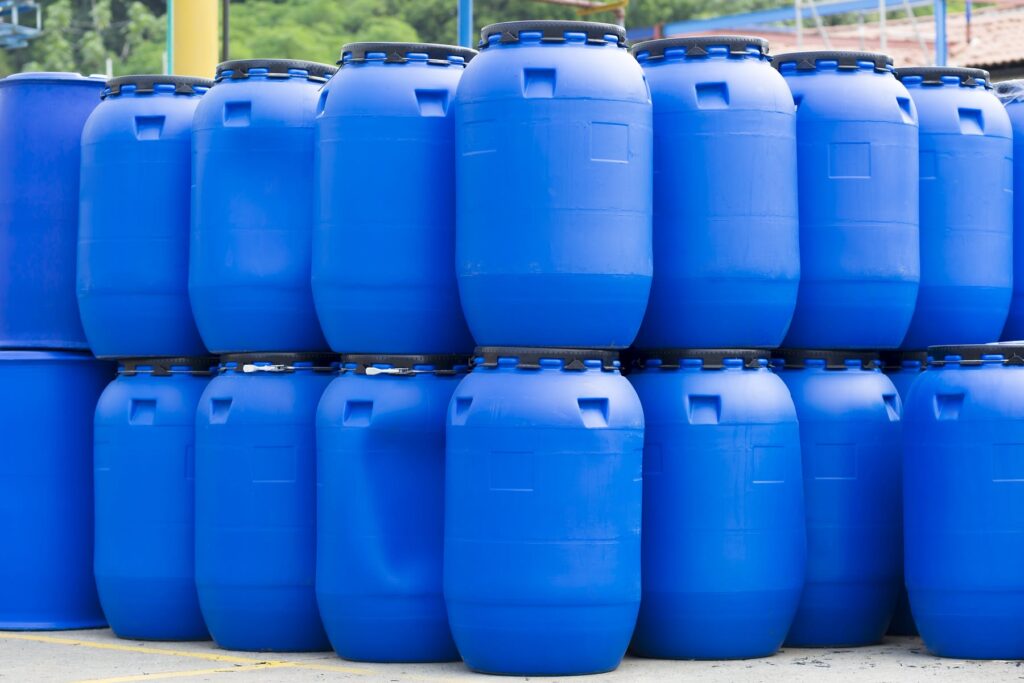
Description du projet abouti : la RFID dans un environnement métallique et liquide
La demande reposait sur deux contraintes majeures en agroalimentaire : l’environnement métallique (la chaîne de production grillagée) et l’environnement liquide (production de levure liquide).
Les puces RFID, placées sur les citernes, ont été développées spécifiquement en tenant compte de l’environnement où elles vont évoluer, gagnant ainsi en performances et garantissant une détection à 100%, nécessaire pour un process fiabilisé.
La contrainte de lavage a également été intégrée dans la conception des puces RFID, elles doivent en effet résister à des nettoyages industriels fréquents sous très haute pression. Pour cela des matériaux spécifiques ont été mis en œuvre et la colle a subi des tests poussés avant validation.
Etapes de mise en place
- Analyse théorique et pratique (POC) de l’environnement
- Conception
- Déploiement
- Tests et validation
Infrastructures choisies : solutions fiables et pérennes pour l’industrie agroalimentaire
La ligne de production et les locaux du client ont été équipés comme suit :
Chaîne de production RFID
La chaîne de production basée sur un convoyeur automatisé est équipée de lecteurs et d’antennes RFID adaptés à l’environnement métallique.
Chariots élévateurs équipés RFID
Les chariots élévateurs qui véhiculent les citernes sont équipés d’une antenne de lecture RFID afin d’identifier la citerne qui est déchargée, transportée ou chargée.
Le système se doit d’être mobile et résistant aux mouvements du chariot et aux chocs.
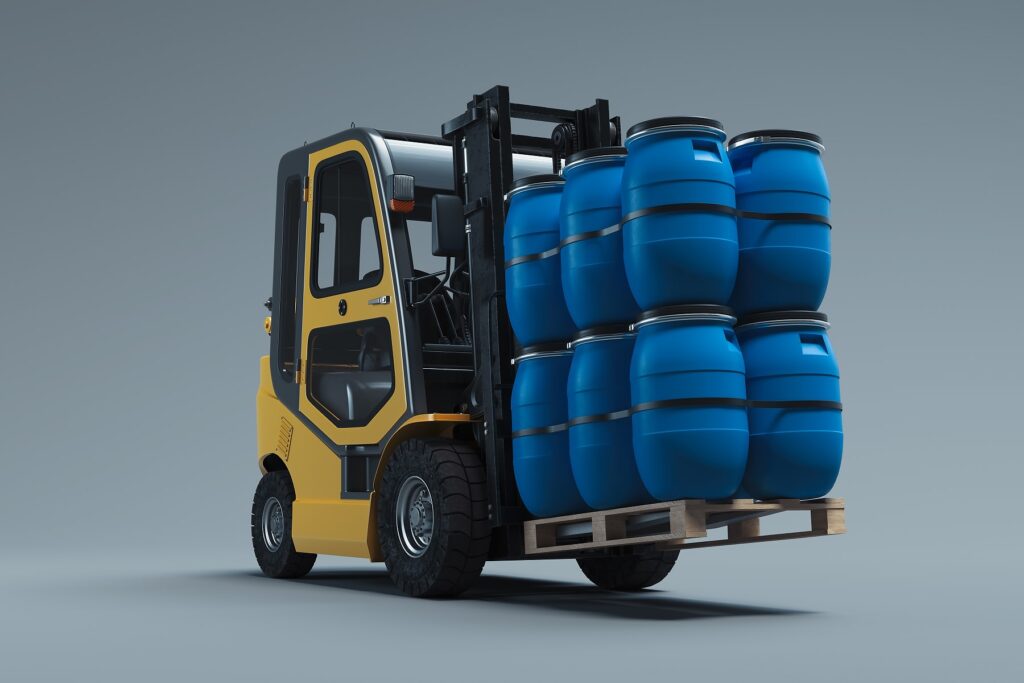
Quais de chargement connectés
Les quais de chargement sont également équipés d’antennes RFID, situées en bord de quai, à l’endroit où le camion vient se placer. Ainsi, lorsque la citerne entre dans le camion, la détection de sa puce permet de vérifier que le bon produit est chargé.
Des antennes RFID intelligentes ont été mises en œuvre : elles sont notamment capables de mesurer le sens de passage, afin de savoir si la citerne est entrée dans le camion pour un chargement ou si elle en est sortie lors d’un déchargement.
Logiciel de pilotage RFID interconnecté à l’ERP
Le logiciel de traitement RFID et de suivi du process a été développé spécifiquement pour le client.
Une interface a été mise en place pour remonter les données dans l’ERP client (SAP).
Avantages de la solution
- Garantir la traçabilité
- Eviter les erreurs de nettoyage
- Avoir une vision temps réel de la production et gagner en réactivité
- Localiser les citernes dans le process et éviter les arrêts de production
- Automatiser la remontée des données dans l’ERP
- Réduire la charge administrative
- Des puces RFID développées sur-mesure, parfaitement adaptées à l’environnement
Découvrez nos auteurs
photo | nom |
---|---|
![]() | Serge WEHRELChef de Projet RF Conception
|